Semiconductors
State-of-the-art with wolfspeed
Wolfspeed is able to achieve material environmental and sustainable benefits from MEGASLAB’s proven durable and impermeable concrete floor slabs.
MEGASLAB Advantages
for Semiconductor Facilities
MEGASLAB’s innovative concrete solutions have significantly elevated the construction and sustainability aspects of Wolfspeed’s new SCF facility. By ensuring longevity, reduced carbon footprint, and operational efficiency, MEGASLAB not only meets but exceeds the demands of modern manufacturing environments. Their partnership with Wolfspeed showcases how strategic construction choices can lead to long-term operational and environmental benefits.
MEGASLAB introduced a high-performance 6-inch concrete slab, compared to the originally specified 9 inches with rebar. It also replaced an ordinary 5,000 PSI slab with a +6,000 PSI MEGASLAB.
This thinner design without rebar allowed for faster prep, placement and curing of the concrete, speeding up the whole construction process. As a result, the entire building timeline was shortened, saving both time and money.
Manufacturing facilities like Wolfspeed’s are places of intense activity, with heavy machinery anchored to the slab and substantial loads moving across the slab 24/7.
Wolfspeed also uses portable robots called automated guided vehicles (AGV) to transport heavy materials around the large industrial space. The AGV traffic and weight create a lot of abrasion on a typical concrete slab, leading to damaged floors.
MEGASLAB provides a more durable surface that can withstand the repeated path of the AGVs due to its higher abrasion resistance.
Ordinary concrete with joints every 12 to 15 feet that curl can cause damage to the wheels of manufacturing equipment like AGVs, leading to premature wear and tear and inefficient operations. Slab repairs and machine maintenance can lead to costly downtime for a facility like Wolfspeed’s.
MEGASLAB’s extended joints remain smooth and virtually curl-free over time, reducing the amount of stress on the machinery for optimal performance and reducing disruptions caused by downtime, enhancing overall operational efficiency.
Wolfspeed’s sustainability commitment is well documented. The company is built on the power of energy-efficient silicon carbide and strives to drive change that transforms communities, industries, and the world by powering more and consuming less.
MEGASLAB enables Wolfspeed to uphold its sustainability commitment since its efficient design results in fewer concrete trucks, less carbon- intensive cement, and no rebar. MEGASLAB’s longer-lasting concrete also reduces the need for repair or replacements, lowering the carbon footprint of the concrete over its lifetime.
In total, MEGASLAB reduced the embodied carbon of the concrete used in the slabs on ground by over 40%. In addition to the lower embodied carbon footprint from the initial installation of MEGASLAB, there will be efficiencies found in daily operations due to the smooth, flat jointless surface.
Wolfspeed required a dense, durable floor slab to ensure operational efficiencies. MEGASLAB was able to deliver an innovative product that achieved this, while also significantly reducing the embodied carbon footprint of the facility.
The MEGASLAB Difference
Increased Durability Strength
Ordinary 5000 PSI slab replaced by 6000+ MEGASLAB with 900+ PSI flexural strength.
2x Life Expectancy
MEGASLAB remains flat and durable for over twice as long as ordinary concrete for less maintenance and downtime and a lower total cost of ownership.
1/3 Reduction in Slab Thickness
Reduction of slab thickness from 9 inches to 6 inches with increased performance and durability.
+ 40% Carbon Reduction
Over 40% reduction in embodied carbon associated with the MEGASLAB concrete system allowing Wolfspeed to claim a reduction in its Scope 3 emissions.
Steel Rebar Eliminated
For faster construction schedules and lower carbon emissions from the elimination of steel rebar.
70% Fewer Joints
For incredibly flat surfaces that remain flat over time, increasing operational efficiencies.
MEGASLAB®
BUILDING A REVOLUTION FOR SEMICONDUCTOR MANUFACTURING
MEGASLAB provided an innovative low carbon concrete slab solution capable of withstanding heavy loads with exceptional durability and resistance against wear and tear. Using MEGASLAB allowed Wayne Brothers to accelerate the construction schedule and provide significant upfront cost-savings.
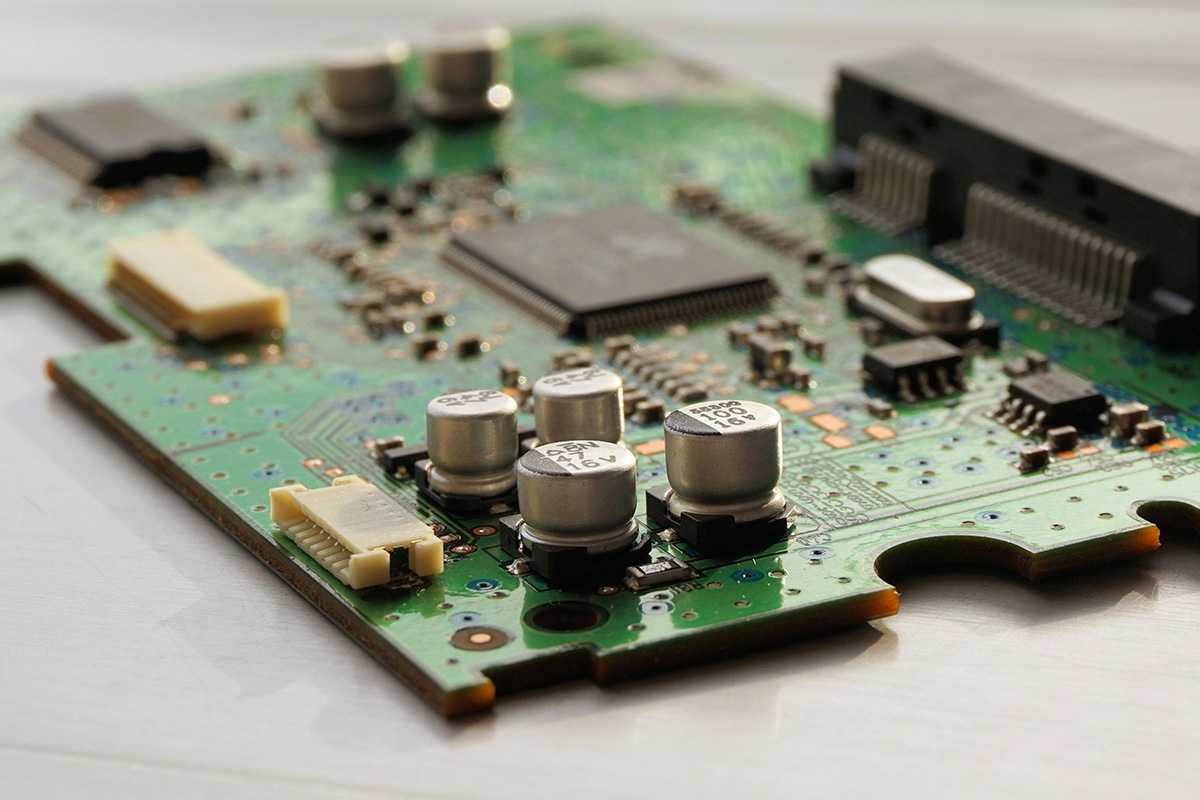
In conclusion, MEGASLAB’s innovative concrete solutions have significantly elevated the construction and sustainability aspects of Wolfspeed’s new SCF facility. By ensuring longevity, reduced carbon footprint, and operational efficiency, MEGASLAB not only meets but exceeds the demands of modern manufacturing environments. Their partnership with Wolfspeed showcases how strategic construction choices can lead to long-term operational and environmental benefits.
Your Semiconductor Project
Needs MegaSlab
Contact us today for more information about building out your project with our revolutionary engineered concrete system.